"Predictive Maintenance in Manufacturing"
"Predictive Maintenance in Manufacturing"
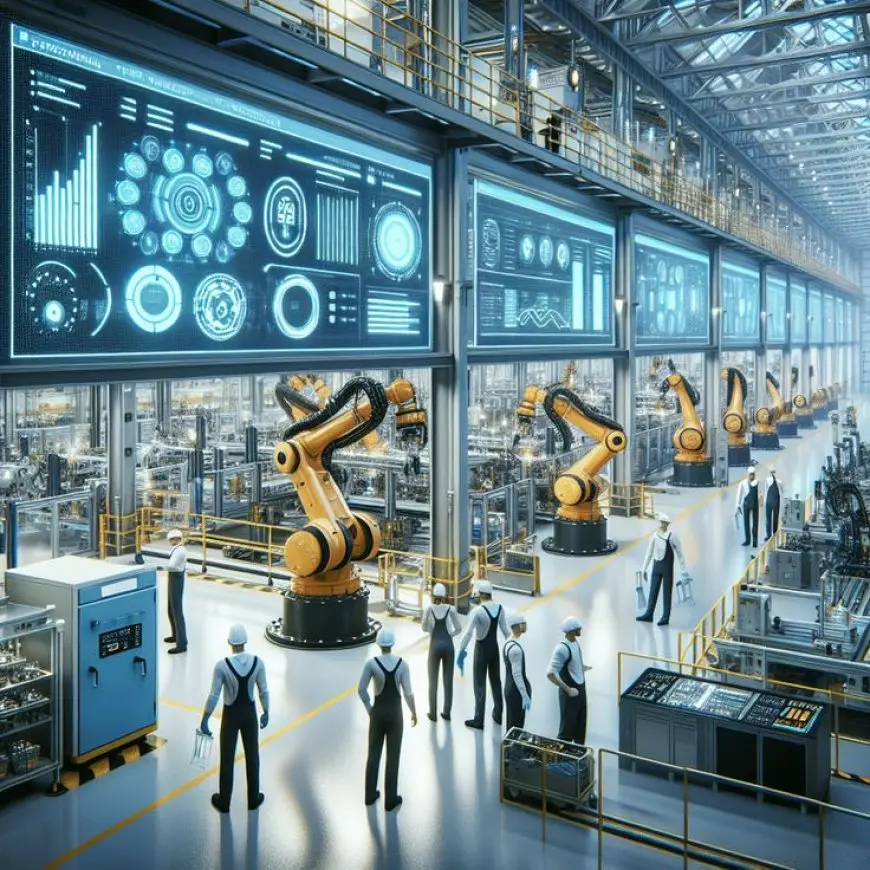
Predictive Maintenance in Manufacturing
Manufacturing is an industry where efficiency, reliability, and cost-effectiveness are paramount. Predictive maintenance (PdM) has emerged as a game-changing approach to equipment maintenance, enabling manufacturers to anticipate and address potential issues before they escalate into costly failures. By leveraging advanced technologies such as IoT, artificial intelligence, and machine learning, predictive maintenance ensures that machinery operates at optimal performance levels while minimizing downtime.
What is Predictive Maintenance?
Predictive maintenance is a proactive strategy that monitors the condition of equipment in real-time to predict when maintenance should be performed. Unlike traditional reactive maintenance, which addresses issues after they occur, or preventive maintenance, which follows a fixed schedule, predictive maintenance uses data-driven insights to determine the precise moment intervention is needed.
How Predictive Maintenance Works
The core of predictive maintenance lies in collecting and analyzing data from machinery. Sensors attached to equipment capture key performance indicators such as temperature, vibration, pressure, and humidity. This data is then processed by sophisticated algorithms that identify patterns and anomalies, signaling potential wear and tear or malfunctions. These insights allow maintenance teams to take timely action, avoiding unexpected breakdowns.
Benefits of Predictive Maintenance
Reduced Downtime: By addressing issues before they lead to equipment failure, manufacturers can significantly reduce unplanned downtime, ensuring continuous production.
Cost Savings: PdM minimizes the need for emergency repairs and extends the lifespan of machinery, reducing overall maintenance costs.
Improved Efficiency: Real-time monitoring helps optimize machinery performance, leading to higher productivity and better product quality.
Enhanced Safety: By identifying risks early, predictive maintenance reduces the likelihood of hazardous equipment failures, ensuring a safer workplace.
Sustainability: Efficient machinery consumes less energy and produces fewer emissions, contributing to greener manufacturing practices.
Applications in Manufacturing
Predictive maintenance is particularly valuable in industries where downtime can be costly, such as automotive, aerospace, and heavy machinery manufacturing. It is used to monitor critical components like motors, turbines, conveyor belts, and hydraulic systems. For example, in a production line, predictive maintenance can detect anomalies in a motor's vibration pattern, prompting repairs before the motor fails and halts the entire operation.
Challenges in Implementing Predictive Maintenance
Despite its benefits, implementing predictive maintenance comes with challenges. The initial cost of setting up sensors, data collection systems, and analytics tools can be significant. Additionally, integrating PdM into existing workflows requires technical expertise and training for personnel. Manufacturers must also address data security concerns, as connected devices may be vulnerable to cyber threats.
The Future of Predictive Maintenance
As technology advances, predictive maintenance is becoming more accessible and effective. The integration of artificial intelligence, cloud computing, and 5G connectivity is enhancing the accuracy and speed of predictive analytics. Moreover, digital twins—virtual replicas of physical assets—are being used to simulate and predict equipment behavior, further refining maintenance strategies.
In the coming years, predictive maintenance is expected to become a standard practice in manufacturing, helping businesses stay competitive, sustainable, and resilient in an ever-evolving market.